Gowning Room Design & Protocol
The proper cleanroom gowning supplies and furniture are essential for cleanroom contamination control. A gowning room, often referred to as an ante-room, is a space outside of the cleanroom in which operators change in and out of street clothes when. The room is divided into a dirty and clean side and optimized for sequential procedures with fewer steps.
Gowning Room Requirements and Applications
Cleanroom gowning requires different furniture and amenities based on the environment at hand. Generally it provides a staging area for sanitation, handwashing, storage, and donning apparel such shoe covers, hair nets (bouffants), gloves, and coats or coveralls.
Gowning rooms for chip fabrication or circuit board assembly areas limit human-driven artifacts such as dead cells, dandruff, hair, and other microparticles. Small particles deposited onto a printed circuit can result in total loss or late evolving defects. ESD fabrics prevent static discharge from damaging sensitive components.
In pharmaceutical, medical, and biotech applications, gowning rooms support passage from uncontrolled common areas to appropriately pressurized cleanrooms. For hazardous or sterile processing, the gowning room design must meet criteria for aseptic workflow, sterilization processes, and operator safety defined under USP, CGMP, or FDA mandates.
A Gowning Area that Supports Clean Protocol
The cleanest cleanrooms dispose of garments after each exit and entry, while cleanrooms with the highest particle thresholds may only change or launder garments twice a week. Here are some common activities and general estimates of particulate generation.
Figure 1: Gowning Area Particle Generators | |
---|---|
Activity | > No. of particles (≥0.3μm) |
Person emits during garmenting process | 3,000,000/min. |
Cleanest skin (hands) | 10,000,000/ft2 |
Employee street clothes | 10,000,000 to 30,000,000/ft2 |
Floor and bench surfaces | > 10,000,000/ft2 |
Garments supplied by cleanroom laundry | 1,000,000/ft2 |
Source: Encyclopedia of Clean Rooms, Bio-Cleanrooms and Aseptic Areas, Dr. Philip Austin, P.E., 2000
Gowning Room Furniture
Workstations and ergonomic furniture are a key piece of comfort over long shifts. Storage lockers, benches, and workstations must fit in small spaces while also supporting safe movement, clean principles, and risk reduction. Furniture and surface requirements differ for unique environments, including but not limited to cleanroom classification, organizational standards, hazards, and product sensitivity. Every aspect of a cleanroom gowning room requires unique surfaces, materials, and and even fixtures for clean-forward use.
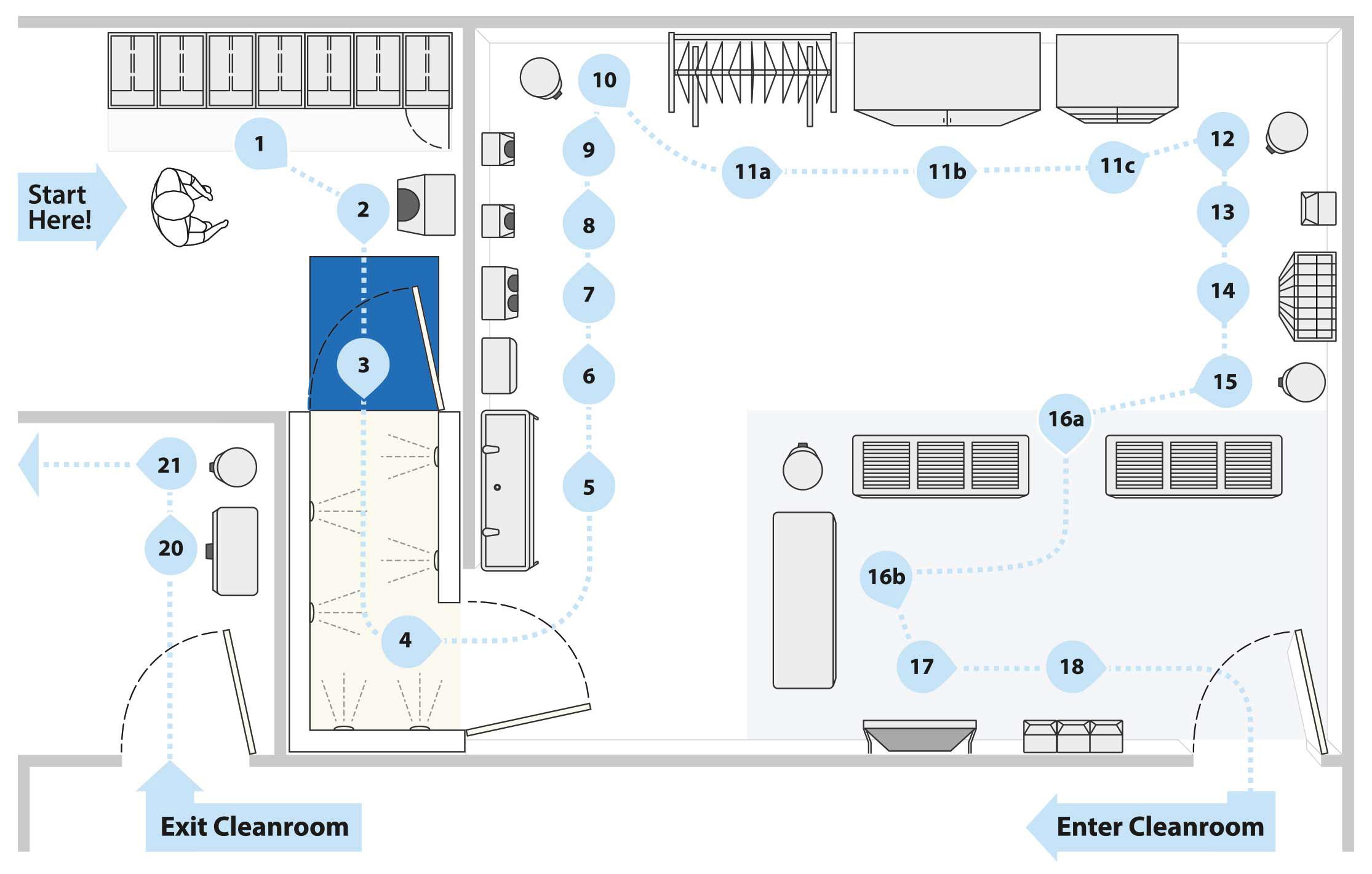
- Secure lockers for clothing and personal property
- Shoe cleaner with rotating brushes to remove gross contaminants
- Walk-off adhesive shoe mat
- Air shower with HEPA filtered air jets to remove loose contaminants
- Hands-free hand washing and hand drying stations with HEPA/ULPA-filtered air
- Dispenser for glove liners or undergloves
- Glove washing and drying station (if gloves not clean)
- Headwear dispenser
- Face mask dispenser
- Waste receptacles should be installed wherever packaging is removed
- Garment storage facility - depends on garment type
- Open garment rack for reusable garments
- Enclosed garment cabinet for reusable garments (includes HEPA blower)
- Garment storage shelves for packaged disposable garments
- Waste receptacle
- Wiper dispenser used to clean bench prior to putting on booties
- Bootie/shoe cover dispenser (can be incorporated into benches)
- Waste receptacle
- Gowning benches for putting on booties. Booties stay on "clean" side
- Cleanroom mirror for final self-inspection (side-by-side with poster showing a correctly garbed model)
- Safety glasses and overglove dispensers
- Air shower - may be required in cleanroom entrance
- Garment hamper for reusable garments to be laundered
- Waste receptacle for disposable garments
Finding the Right Garments and Furniture
A gowning room has many variables. There is no mathematical formula when determining which features, surfaces, and HVAC requirements best suit your facility. Space requirements, volume of operators, aseptic requirements, material compatibility, and even aesthetics all factor into design considerations. Most facilities benefit from contacting a controlled environment specialist who can identify critical product sensitivities and the proper equipment.
Why Buy Gowning Room Design and Equipment from Us?
Production Automation Corporation is a trusted source of general and critically manufactured furniture, garments, gown, and PPE materials. Our customers enjoy nearly unlimited selection, localized delivery programs, and in-stock items that ship quickly from regional warehouses.
We provide a one stop shop for gowning room products with easy navigation controls for selecting your particular classification or process demands. Some crucial aspects of gowning furniture requirements are often under considered. For example, the distance between a sink and a critical surface, the location of a hazardous storage cabinet, or the number of air changes per hour is often determined on a case-by-case basis. Our application specialists are here daily for phone, email, and chat support when you need help with a selection.